The Commercial Painting Industry Association again partnered with Technology Publishing Company for the seventh annual commercial honors program, The Elevation Awards.
The awards recognize projects ranging from residential exteriors and commercial renovations to floor coatings and wallcoverings throughout the commercial coatings industry.
This year’s group of outstanding projects, completed between Jan. 1, 2022, and July 10, 2023, represented an impressive collective of not just commercial painting contractors, but also architects, interior designers, decorative artisans, manufacturers and suppliers throughout the industry.
Projects were reviewed and assessed by our panel of industry expert judges, including:
-Michael Capulong, Colour Studio;
-Andre O. Desjarlais, Oak Ridge National Laboratory;
-Brian Jurgens, W.T. Kenney Company, Inc.;
-Jeff Theo, Vulcan Painters; and
-Ken Trimber, KTA-Tator, Inc.
The 2023 Elevation Award Winners are as follows:
New Construction: Muckleshoot Indian Tribe Community Center
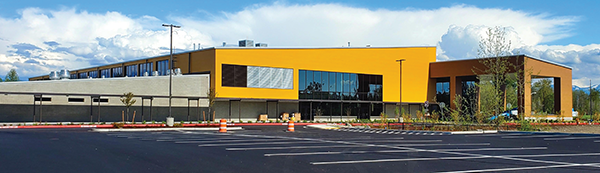
Project Location: Auburn, Washington
Contractor: Merit Construction
Facility Owner: Muckleshoot Indian Tribe
Material Suppliers: Evonik, Rodda Paints
When the Muckleshoot Indian Tribe put out a bid for painting work on a new community center in Auburn, Washington, Alyssa Sullivan of Sullivan Painting said her company was eager for the chance to perform one of its largest projects to date.
But when the company was awarded the project, her father, Sullivan Painting owner Kevin Sullivan, was sadly in the hospital recovering from a severe motorcycle accident.
Alyssa realized that the company would have to focus on an “extremely difficult” design-build project with an accelerated schedule—but she says her painters rose to the challenge in honor of her father.
“Our crew put their hearts and soul into completing this project with the highest of expectations to ensure we could still make Kevin proud while he was at home healing,” she added.
The vast scope of work wasn’t the only challenge faced once the project began. Much of the steel for the pre-engineered metal building came raw from the factory instead of pre-primed, so Sullivan said the crew spent weeks simply cleaning the steel just to get it ready for priming. Between cleaning, priming and finish coating, the gym ceiling alone took over three months to complete.
“The gym ceiling looks to have been completed with care and detail," said Michael Capulong, one of the award judges. “And the yellow exterior is powerful!”
The walking track railing around the gym also had to be painted after installation because it needed to be welded in place. However, the project foreman found that the pre-primed mesh panels had major adhesion issues—which Sullivan says caused the primer “to fall off in your hands.”
The foreman ordered the panels to be cut down, blasted, reprimed and re-installed, which pushed the painting of the railings right into the middle of the walking track installation. The painting contractor utilized coating systems from Evonik and Rodda Paints.
Two of the judges praised the contractor for successfully adapting once the problem was identified. “It was impressive to see the contractor uncovering and correcting problems as an integral part of the team,” said Trimber.
“It’s always challenging when the change orders probably exceed the original project scope,” added Desjarlais.
Sullivan said that “trade stacking was inevitable” with the tight project schedule, and calculated that over 300 hours were spent on trade damage touch-up. However, because of this, she said that all of the workers from the different trades “developed great relationships by the end, because they worked so closely together on the entire project.”
In fact, the project superintendent from general contractor, Merit Construction, commented that “professionalism and safety were always right up there with production, and [the company] certainly proved that these facets of the trade were not compromised with a job of this size.”
Mixed-Use Commercial: Pier One Sydney Harbour Hotel
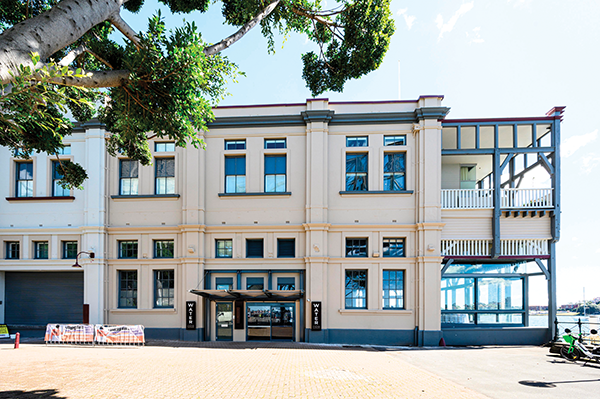
Project Location: Sydney, Australia
Contractor: Higgins Coatings
Facility Owner: Marriott
Material Suppliers: Dulux Paints
With a rich history dating all the way back to the late 1800s when it served as barracks and later as a busy commercial wharf, the Pier One Sydney Harbour in Sydney, Australia, was repurposed into a hotel in 1998 and is now managed by Marriott under its Autograph Collection portfolio.
In recent years, the exterior of the building had begun to deteriorate and needed a repaint to restore life to the facility. However, significant remedial issues—including failing concrete spalling, timber issues, render cracking, damaged glass, and flashing throughout—also needed to be addressed before painting could begin.
To make matters worse, the project scope contained one final caveat: the hotel needed to remain open and as close to fully functional as possible.
According to Vesnel Fresnido of Higgins Coatings, the company was brought onto the job by project management firm The Project Studio based on Higgins’ experience with performing restoration work while minimizing disruption to the facility’s daily operations.
The Higgins team came up with an operations plan that included over 1,700 liters of concrete spalling, 25 timber remediation repairs, 280 square meters of render repairs, and the replacement of 28 glass panels and 130 meters of flashing.Finally, three coats of Dulux Acratex Acraskin, which allows for expansion in the masonry while protecting the façade from moisture ingress, were applied to the building’s exterior.
“The material finish looks great on the building; it’s very clean yet inviting,” said Capulong.
The Higgins operations team used scaffolding, rope access, and scissor and boom lifts to safely access all surfaces. The fixed scaffolding was cloaked with an Envirocloth wrap to keep paint residue from entering the surrounding waterways. Traffic control measures were also implemented to keep pedestrians safe from all operations.
Fresnido credited Glenn Johnson of The Project Studio and his team for their “invaluable” oversight throughout the upgrade process, and said that the Higgins’ remedial work “provided a canvas for [the] external repaint that has rejuvenated the facility in full.”
Desjarlais agreed, adding that “focusing on refurbishment prior to refinishing is the correct path.”
Multifamily/Residential High-Rise: Trump Hollywood Condominium
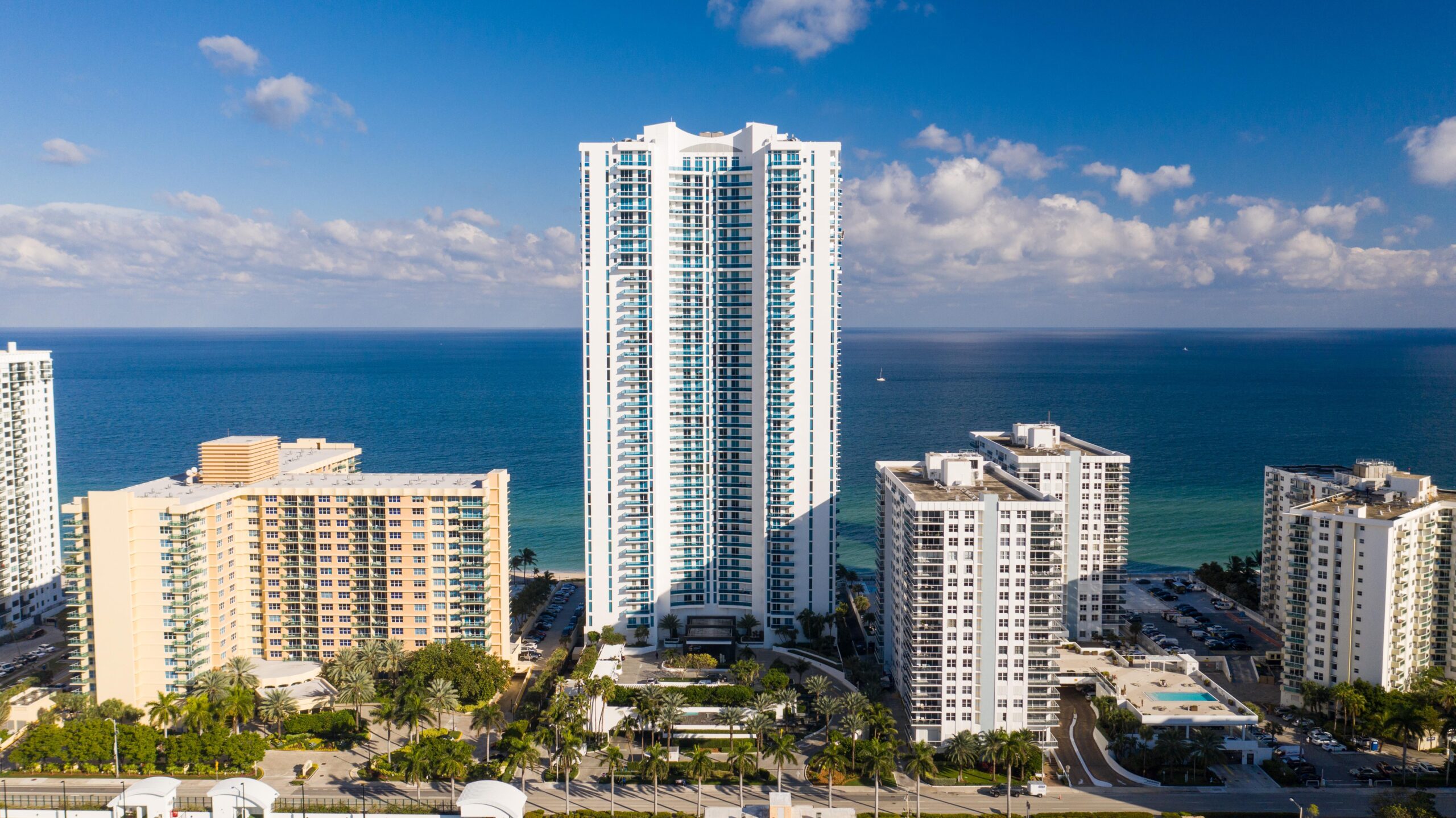
Project Location: Hollywood Beach, Florida
Contractor: Capital Contractor Services
Facility Owner: 2711 Hollywood Beach Condominium Association
Material Suppliers: APV Engineered Coatings
Located on a picturesque oceanfront location in Hollywood Beach, Florida, the 41-floor Trump Hollywood condominium building embodies South Florida luxury. However, as with virtually every building located in coastal Florida, the building’s exterior is exposed daily to punishing environmental conditions including high UV rays, high humidity, salt spray and windborne sand.
Over the years, these environmental assaults served to break down the builder-applied acrylic coating on the building’s stucco surface, leaving it chalky and dull and exposing the underlying substrate to damage from the elements.
Capital Contractor Services was engaged to give the luxury building a facelift and restore its luster—a project that would involve more than just a fresh coat of paint.
Ultimately, the scope of work for the 18-month project included:
-A full-building inspection to identify areas where delaminated stucco needed to be replaced;
-Replacement of delaminated stucco;
-Power washing of all stucco surfaces to remove dirt, salts and other surface contaminants;
-Scuff sanding of factory-finished aluminum window and sliding door frames to remove corroded metal;
-Removal and replacement of sealants surrounding the window/door frames;
-A 100-square-foot mock-up on the ground level to test surface adhesion, inter-coat adhesion, mil thicknesses and color-/sheen-matching against project specifications;
-Roller application of two coats of NeverFade W-1500 Primer (total 1 mil dry thickness) and one coat of NeverFade Original Restoration Topcoat (total 2 mil dry thickness) to all stucco surfaces; and
-Roller application of two coats of NeverFade W-1650 Bonding Primer and one coat of NeverFade Metal Restoration Topcoat to all metal window and door frames.
According to the project nomination, the Capital crew took special care to limit inconveniences to residents and ensure their safety throughout the project. When and where possible, they restricted residents’ ground access in the areas being worked on.
Where that wasn't possible, such as in pool and beach walkway areas and active driveways, Capital utilized overhead scaffolding with netting or plywood to protect residents and vehicles. The coatings’ low VOC content and low odor also kept tenant inconvenience to a minimum.
“The unique angles of the high-rise building made access a challenge,” said Alex Forjan, executive vice president of the exterior division at Capital. “We used swing stages and vertical line drops to complete each section of the building with rollers to eliminate the need to lug heavy spray equipment and avoid the potential for windborne spray.”
To maintain project site safety during coastal storms that packed high winds, Capital completely de-mobilized the project—removing all equipment—and remobilized four times through the project.
“Trump Hollywood’s name-brand prestige, size, unique shape and location, coupled with the fact that it was occupied by residents who didn’t want to be inconvenienced during the façade restoration process, made it imperative for us to work deliberately, safely and with a high level of quality,” said Forjan.
Forjan also noted that it was important to use coatings that would look good when applied and would provide long-lasting performance.
They selected APV Engineered Coatings’ line of NeverFade Exterior Restoration Coatings containing Kynar Aquatec, a water-based polyvinylidene fluoride (PVDF) resin that has the ability to resist film erosion, chalking and fading caused by harsh UV exposure.
After work was completed, final walkthroughs with building management, the building maintenance supervisor, City of Hollywood Building Department, and owner representative Paramount Consulting confirmed that the project successfully met the specifications.
Now, thanks to the Capital crew’s careful coating selection and application, the Trump Hollywood has a clean, fresh exterior in a custom-color matched shade of white, with a high level of gloss to make the white pop.
Institutional: Principia School Natatorium
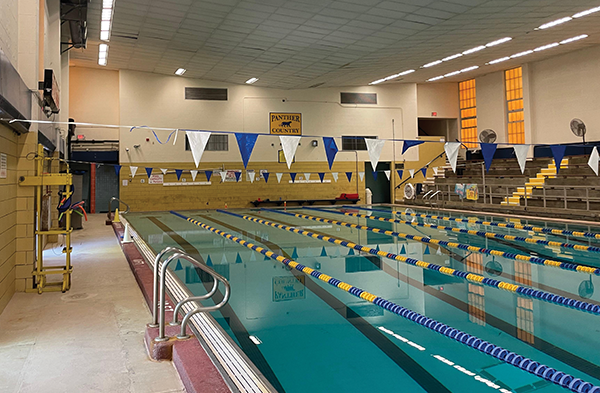
Project Location: Town and Country, Missouri
Contractor: Helmkamp Construction
Facility Owner: Principia School
Material Suppliers: Sherwin-Williams, Tnemec
In May of 2023 Bazan Painting was tasked with providing a much-needed face-lift to the indoor pool area of the Principia School, a college preparatory academy in Town and Country, Missouri.
The natatorium was composed of worn-out glazed block that had discolored and oxidized over time, and Eric Hellwig of Bazan Painting noted that painting glazed block is no easy task.
On top of that, Principia hadn’t contacted Bazan about the project until the beginning of May but needed this sizable project completed before the end of June—leaving an unusually short time period for the work to get finished.
The Bazan crew wasted no time tackling the expansive scope of work, which included pressure washing and acid washing the tile pool surfaces, re-caulking all joints in the pool, re-painting the deep water warning stripe in the pool and footholds for the ladders, and painting the diving boards, diving board bases and gutter grates with Tneme-Fascure 161 from Tnemec.
The crew also prepped, patched and coated the pool deck and curb surrounding the pool, as well as the stairs at the spectator viewing area, with Sherwin-Williams H&C Colortop Water-Based Deck Coating.
In addition, the workers had to restencil all pre-existing depth markings on the pool deck. In the spectator area, the crew sanded, patched and painted the worn-out wooden benches to a vibrant blue color, giving a fresh new look with the aid of Sherwin-Williams Water-Based Catalyzed Epoxy.
The block needed to be scuff sanded before applying a bonding primer that would allow the water-based epoxy to adhere to the block. In addition, all of the metal convector covers above the glazed block walls were starting to rust andcorrode, so the crew prepped and painted these with Sherwin-Williams Waterbased Alkyd Urethane.
Hellwig said his skilled craftsmen “completely knocked it out of the park” and were able to get this project completed before Principia’s target date of June 23.
“With the partnership of Helmkamp Construction, we were able to successfully complete this project on time and deliver a quality product to the customer,” said Hellwig.
“Nice job on a very tight time schedule. Preparing and painting glazed block can be very challenging, but it looks like they did it successfully,” added Trimber.
Floor Coatings: St. Joseph Catholic Church
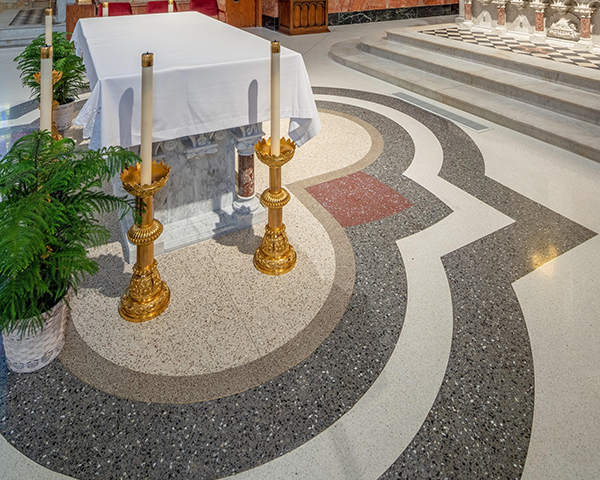
Project Location: Jasper, Indiana
Contractor: Midwest Terrazzo
Facility Owner: Evansville Catholic Diocese
Material Suppliers: Sherwin-Williams Flooring
For three months in 2022, an installation crew from Midwest Terrazzo worked on installing a highly polished, decorative terrazzo floor that complements the newly renovated St. Joseph Catholic Church in Jasper, Indiana—bringing additional beauty to the already picturesque, Romanesque Revival-style place of worship.
The new floor was almost not a part of the nearly $10 million renovation project, but structural foundation issues forced the church to remove the existing cement terrazzo floor installed in the 1950s.
In its place, the Evansville, Indiana-based flooring contractor created an 8,500-square-foot, multi-colored thin-set epoxy terrazzo floor featuring marble and mother of pearl aggregate with distinctive medallion inlays and patterns fashioned from brass divider strips.
The flooring installation presented its share of challenges—from a tight project time frame for completing a new decorative floor from scratch to working in a 143-year-old structure with unsquared corners and walls.
Midwest Terrazzo worked with the church, the project architect and Sherwin-Williams to review and approve the flooring’s unique color scheme. Sherwin-Williams provided a wide array of color samples, which Midwest Terrazzo formed into mockups for approval.
Once finalized, Sherwin-Williams kept these colors on file for rapid production when installers needed material. The store even supplied 50-gallon drums of certain resin colors to reduce handling, mixing and installation times at the project site.
“Almost no one does cement terrazzo anymore, so it’s becoming a lost artform,” noted Graham Wink, President, Midwest Terrazzo. “But we were prepared to take on the challenge and had even ordered some materials and started some training clinics at our shop with a we were prepared to take on the challenge and had even ordered some materials and started some training clinics at our shop with a seasoned installer to get up to speed.”
Thanks to the dedicated work of the contractor’s skilled craftsman, combined with the use of efficient, easy to apply products from Sherwin-Williams High Performance Flooring, Midwest Terrazzo finished the floor on time in September 2022, enabling additional construction crews to finalize the interior renovations rapidly thereafter.
The church was able to meet its goal of welcoming parishioners to the newly restored sanctuary in time for the 2022 Christmas season, and the new thin-set epoxy terrazzo flooring could very well last as long as the structure has already been around, giving a second lifetime to the magnificent historic church.
“Beautiful restored flooring,” commented Desjarlais. “It’s always a major challenge to perform a retrofit.”
“Midwest Terrazzo clearly knows what they are doing,” added Trimber.
Ancillary/Misc. Services: Amblebrook Wellness Center
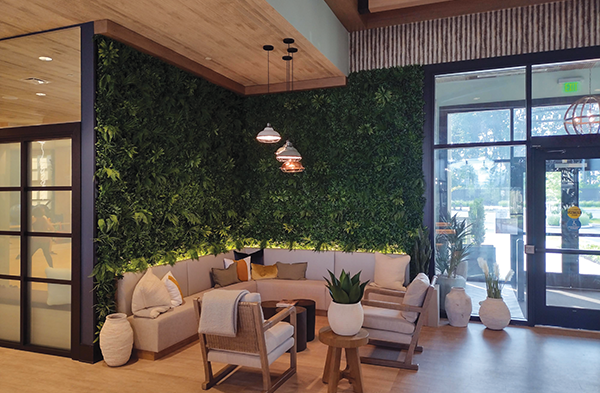
Project Location: Gettysburg, Pennsylvania
Contractor: Brehbill & Helman Construction Co., Inc.
Facility Owner: CCD Rock Creek, LLC
Material Suppliers: Brewster, Koroseal, Lovesdesign, Milton & King, Phillip Jeffries
Amblebrook Wellness Center is the newly constructed centerpiece of a 55+ active adult community located in Gettysburg, Pennsylvania. According to Beth Peiffer of Ralph E. Jones, Inc. (REJ), this wellness center is “the focal point of this ever-growing community and the thread that binds the community together in terms of social, physical, mental and spiritual activities.”
REJ was selected to perform the wall covering installation, including wood effect wall covering on ceilings and custom graphic wall coverings, and paint and coatings application.
The scope of work called for more than 20 different wall coverings and paint application systems, and the facility owner required a quick turnaround—leaving a short duration to complete a project of such size and complexity.
In addition to the scheduling, the REJ team overcame numerous challenges during the course of the Amblebrook project, according to the nomination.
Obstacles included humid conditions and the need to apply coatings to beams above a full swimming pool. This meant that custom wallcovering quantity and sizing decisions required "perfection" to successfully complete the project, according to the contractor.
“This was an interesting use of multiple coverings in a single facility,” said Desjarlais.
On top of it all, REJ mentioned that it experienced field crew shortages throughout the job—a challenge Trimber acknowledged is an industry-wide issue many other contractors struggle with.
“Nice job, aesthetically pleasing. They mention a legitimate problem in finding skilled craftsmen for the work, but overcame the challenge,” he noted.
Once the project was completed, an open house was held. According to the contractor, the final result was “well received and much welcomed” by the local community.
Judges' Choice: John Marshall House
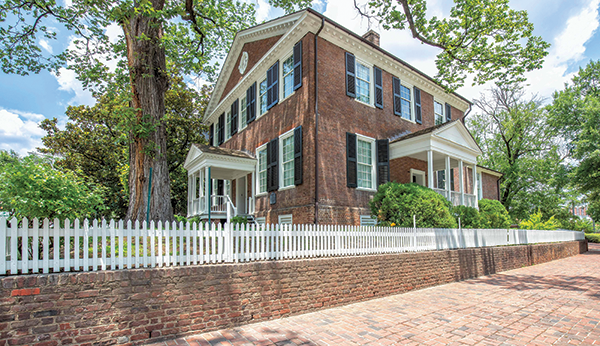
Project Location: Richmond, Virginia
Contractor: Widespread Solutions
Facility Owner: Preservation Virginia
Material Suppliers: Sherwin-Williams, deGruchys Limeworks, Sarco Putty
Virginia-based painting contractor Widespread Solutions had the unique opportunity to help restore the exterior of the John Marshall House, a historic house museum and National Historic Landmark in Richmond, Virginia.
Built in 1790, it was the home of Chief Justice of the United States and Founding Father John Marshall, who was appointed to the court in 1801 by President John Adams.
According to Daniel Payne of Widespread Solutions, the project was challenging due to its present-day location in bustling downtown Richmond as well as the difficulty of reconstructing and matching historical exterior finish elements of the house.
On the carpentry side, the scope of work included trim removal and replacement, with custom-milled soffit, fascia and rake boards made by a local millwork company to match the building’s unique profile. The knives that cut the wood to craft the profile were made specifically for this home, and the millwork was matched perfectly, according to Payne.
For joint reconstruction and restoration, the previously installed silicone caulking at the window frame and brick joint was removed, and a natural hydraulic lime product was used to infill the joint. Payne said that this application promoted the reproduction of historical-era construction and sealants.
Window sashes were completely removed and meticulously shop-restored, with over 30 panes of era-specific bubble glass shipped in from Maryland. Each window was re-glazed using Sarco Multi- Glaze Type-M Glazing Compound.
Following shop priming and painting of the building exterior, the windows were re-installed.
The team also carefully removed, repaired and painted all of the building’s shutters at its shop. Payne commented that it was “a true joy to work on an element of this home that was completely and originally constructed using dowels as the fasteners,” noting that there were no nails used on these historic shutters.
For exterior surface-prep and painting, the home was soft-washed and hand-tool-prepared. One full coat of Sherwin-Williams Prep Rite Pro Block Primer was applied to all substrates, and a finish coat of Sherwin-Williams Duration Satin was applied until the manufacturer’s recommended coverage was achieved.
Access was no small task throughout the project, said Payne. The Widespread Solutions crew used an X600AJ Compact Crawler Boom Lift from JLG to reach all elevated areas.
The Elevation Awards judges were unanimous in their praise of the finished product.
“Great job preserving the historical façade; the work is very intricate. Each element of the home looks masterfully completed,” said Capulong.
“The attention to detailing on a historical landmark is laudatory. My favorite,” commented Desjarlais.