Specialty chemicals company Arkema recently announced that partially or fully recycled polyamide products are being produced at its custom recycling center in Italy. Now available through the Virtucycle program, Rilsan polyamide 11, Rilsamid polyamide 12 and Pebax polymers are being commercialized.
“More and more, our customers are interested in innovative recycled options in order to drive improved sustainability and circularity in the supply chain,” said Erwoan Pezron, Arkema’s Senior Vice President for High Performance Polymers.
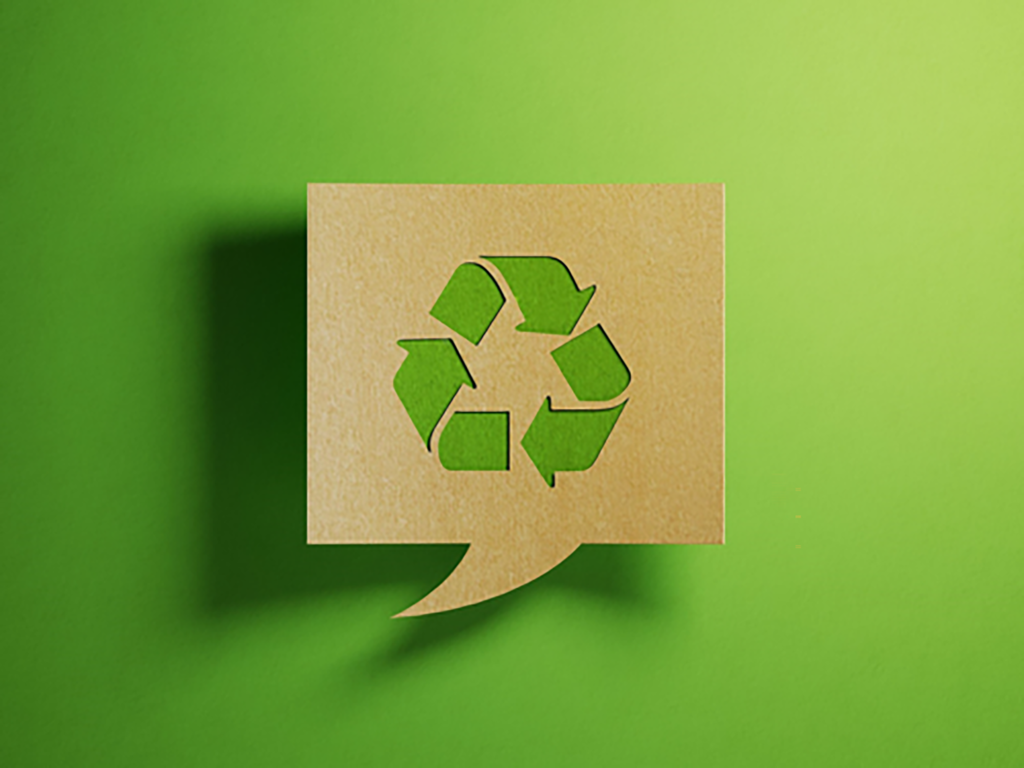
About Virtucycle
Launched in October 2019, Virtucycle aims to develop circuits for the collection and regeneration of Arkema products in partnership with Agiplast. Specifically, the program focuses on polyamide 11 and polyamide 12 resins, PEBA elastomers, and PVDF fluoropolymers.
Arkema reports that it acts as a kind of “match-maker” for sourcing materials to be recycled and matching those materials with customers who desire partially recycled grades with a more favorable LCA profile.
Manufacturer customers have an option to build closed circuits, where the product is recycled to be reused by the same customer, or open circuits, where the company provides the customer with grades of recycled polymers that may come from other markets or applications.
“This is perfect for our polymers, which have exceptional durability, while minimizing CO2 impacts compared to other recovery technologies. Recycling a polymer according to the Virtucycle program can allow a reduction of more than 70% of greenhouse gas emissions compared to the original production of the polymer from its component raw materials,” said Charlotte Herdt, Sustainable Development Expert in charge of the Virtucycle program.
“The impact on CO2 emissions visualized in the life cycle analysis is therefore remarkable. Our strategy is to produce polymers containing a part of recycled material which achieves an excellent level of quality for the targeted industrial application. This allows us to offer a performance guarantee at the same time as higher volume under a recycled label, which responds to a genuine market expectation and a solid contribution to sustainable development in the polymer industry.”
Additionally, Arkema is reportedly working with some major brands on projects for the recovery of end-of-life products, including the creation and optimization of cost-effective collection networks. Since its launch, Arkema reports that the initiative has generated numerous pilot projects in several markets.
New Recycled Products
By the end of this year, Arkema is aiming to offer several SCS certified grades that will meet critical performance standards while also offering a traceable supply chain. The grades are produced at Arkema’s custom mechanical recycling center for advanced polymers in Italy using only renewable energy.
Detailed LCA data packages will reportedly be available upon request.
Arkema acquired Agiplast, a company specialized in the regeneration of high performance polymers and its historical partner in recycling operations, in 2021. Operating in Italy, the plant employed 32 workers at the time with annual sales of around 15 million euros.
“With the recent acquisition of Agiplast, we were able to take a quantum step in the right direction by marrying our legacy polymer design expertise with the advanced recycling capabilities of Agiplast as well as our extensive global network of customers with ambitious commitments to sustainability,” said Pezron in the press release.
“The ability to design certified recycled grades with high performance and lower carbon footprint is an exciting step in the sustainability journey of our customers and Arkema. Extending the life of these polymers, sometimes in applications quite unrelated to their original use is gratifying. The growth potential is significant.”
Last month, Arkema also announced the certification of a range of bio-attributed acrylic monomers using the mass balance approach. The company reports that these monomers allow them to start offering certified bio-attributed specialty acrylic additives and resins for a wide range of applications.
Certified under the International Sustainability and Carbon Certification-PLUS (ISCC+) framework, the new range reportedly supports Arkema’s customers in achieving their climate plan goals by reducing their scope 3 greenhouse gas emissions.
“The development of these bio-attributed acrylic materials is an important step on the sustainable development roadmap of Arkema and its Coating Solutions segment,” said Hervé Castres Saint Martin, Global Group President Acrylic Monomers.
“These innovative products deliver the same high quality and performance that our customers expect from us, while at the same time enabling them to lower their own carbon footprint.”
The mass balance chain of custody is designed to track the total amount of the content in scope through the production system and ensure an appropriate allocation of this content to the finished goods based on auditable bookkeeping.
This approach reportedly complements the bio-based segregated polymers, resins and additives Arkema is already offering, including Rilsan and Pebax Rnew polyamide 11 advanced polymers, Sartomer Sarbio UV-curing resins, Synaqua alkyd emulsions, Crayvallac and Coapur rheology additives.
Circular Plastic Recycling Project
In September, Arkema announced that it is joining a consortium of Spanish companies to enhance the recyclability of post-consumer plastics and tires to reuse for powder coatings. The project aims to improve circularity by using renewable monomers and polymer upcycling.
Dubbed SusChemPol, the innovation project looks at generating more sustainable chemical recycling strategies to obtain value-added molecules and monomers from waste. The project, which began September of last year and runs until September 2024, reportedly stands for “enhancing circularity by using renewable monomers and sustainable chemical strategies of polymer upcycling.”
According to the project’s website, plastic and end-of-life tires (PET) are one of the most significant issues facing waste management today. About 40% of post-consumer plastic packaging reportedly ends up in landfills, within only 2% of all recovered plastic packaging reused for applications of the same or similar quality.
Plastics are found in water, soil, and even biological organisms, SusChemPol reports, due to the annual growth in global polymer production consistently outpacing global gross domestic product and population growth. A study earlier this year found that paint alone accounts for 58% of microplastics in the world’s oceans and waterways.
The project focuses on four main objectives:
-Develop profitable and sustainable chemical recycling alternatives with scalable potential based on chemolysis, chemocatalysis, thermolysis and devulcanization processes to recover three main polymeric waste: polyesters, polystyrene and derivatives and rubber;
-Ecodesign alternative synthesis strategies to produce polymers (particularly polymer networks) that can be recycled and reused;
-Evaluate the material upcycling of recycled and renewable monomers, transforming them into new polymers, coatings or more sustainable products with high added value; and
-Develop predictive models to assess the quality of chemically recycled monomers/oils from complex mixtures of multiple materials found in real waste streams
With this research, the team hopes that plastics from water bottles or other plastic items can be reused as raw materials for more sustainable polyester powder resins in the coating market.
Arkema reports that powder coatings are well positioned to further sustainability across household and industrial applications, including home appliances and furniture, automobiles, sports stadiums and more.
The coating process is reportedly optimized to produce a high-quality finish while using the minimal energy, minimum waste and time, with the powder that doesn’t end up on the product able to be collect, recycled and potentially reused.